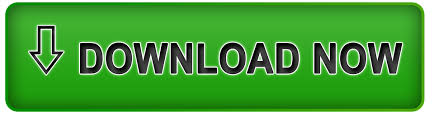

Ben Salem, Numerical analysis of the behavior of a new aeronautical alloy (Ti555-03) under the effect of a high-speed water jet, China Ocean Eng. Bruce, Hydrodynamics and fluid-structure interaction by coupled SPH-FE method, J. Sun, Fully-coupled fluid-structure interaction simulation of the aortic and mitral valves in a realistic 3D left ventricle model, PLoS One. Wenjun, Abrasive waterjet machining simulation by SPH method, Int. Fukagawa, Numerical simulation of soil–Water interaction using smoothed particle hydrodynamics (SPH) method, J. Hosseini, An incompressible SPH method for simulation of unsteady viscoelastic free-surface flows, Int.

Lush, Comparison between analytical and numerical calculations of liquid impact on elastic-plastic solid, J. Cornier, Numerical simulation and experimental study of the interaction between a pure high-velocity water jet and targets: Contribution to investigate the decoating process, Wear. Al-Hassani, An explicit numerical modeling of the water jet tube forming, Comput. Barrett, Experimental and numerical study of water jet spot welding, J. Nguyen, A numerical study on high-speed water jet impact, Ocean Eng. Ammarab, Development of a numerical model for the understanding of the chip formation in high-pressure water-jet assisted machining, Finite. Humrutha, Review of computational fluid dynamics studies on jets, Am. This work is supported by the University of Monastir (Tunisia).Ĭompeting Interests: The authors declare no competing interests. These comparisons serve not only to validate the numerical simulation but also to give guidance in formulating the SPH-FEM numerical model. It is demonstrated that the CEL method presents smoother curves compared to the SPH method. Results of the coupled SPH-FE simulation were further validated. A Numerical model was developed using ABAQUS/Explicit version 6.14. The distribution of the pressure on the impact surface and the resulting deformation of the structure were discussed. To model the entire process, the SPH method was used to model the water jet and the FE method for the PMMA structure. A water jet with a spherical head was used at an initial speed of 570 m/s to impact a flat plate made of Polymethyl-Methacrylate (PMMA). Numerical results are compared with the results of another simulation carried out by the CEL (Coupled Eulerian-Lagrangian) method. In this paper, we present a numerical simulation of a round impacting jet using coupled Smoothed Particle Hydrodynamics (SPH) and Finite Element (FE) methods.
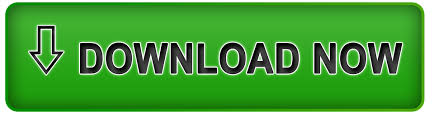